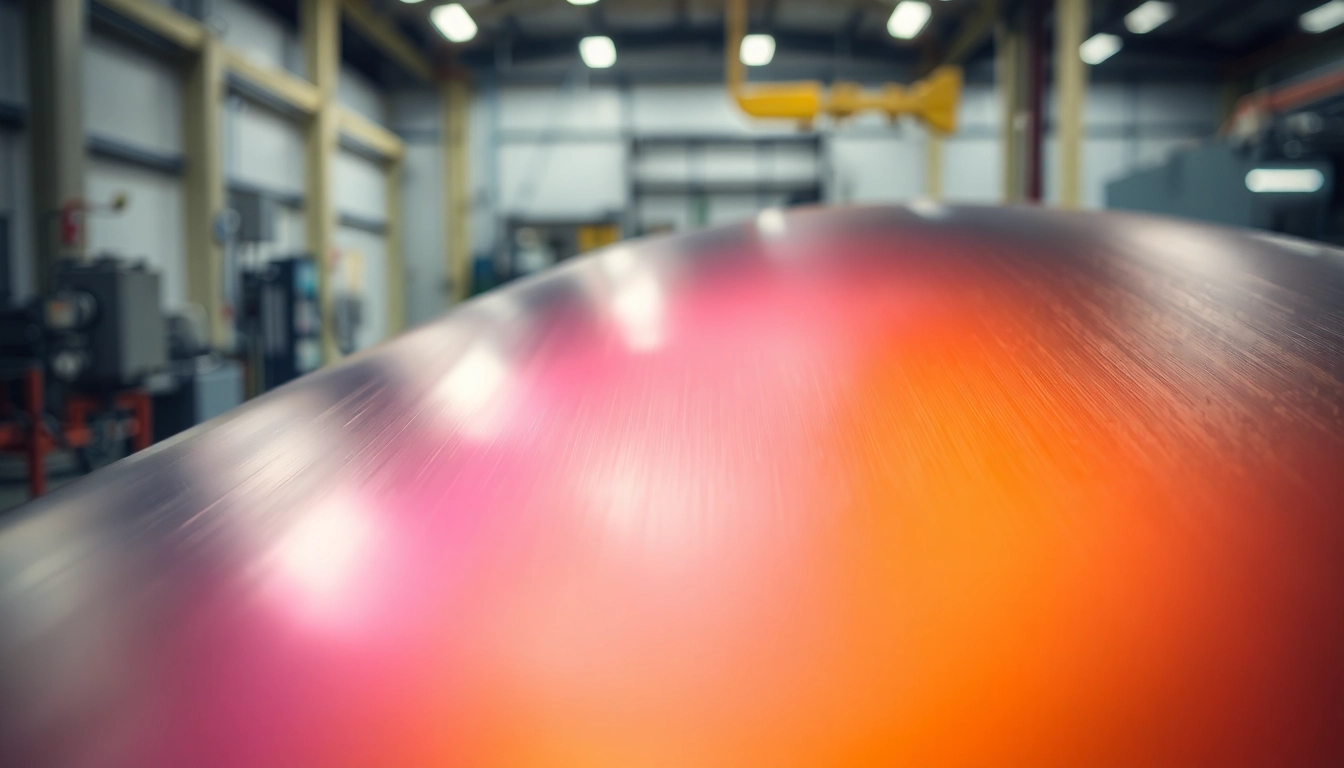
Introduction to EP Coating
Electrophoretic coating, commonly referred to as EP Coating or E-Coat, is a modern surface finishing technique that enhances the durability and performance of metal components. This innovative process leverages the principles of electrochemistry to provide a uniform and efficient coating of various substrates, primarily metals. EP Coating has gained widespread recognition across multiple industries for its excellent corrosion resistance and is increasingly utilized in automotive, industrial, and consumer goods manufacturing. In this comprehensive guide, we will delve into the intricacies of ep coating, exploring its applications, benefits, processes, and the future of this technology in the manufacturing landscape.
What is EP Coating?
EP Coating is a process that uses an electric current to induce a chemical reaction, resulting in the deposition of paint or other coatings onto conductive substrates. The technique involves submerging the substrate in a paint bath that contains charged pigment particles. When an electric current is applied, these particles migrate towards the substrate’s surface and bond to it, creating a durable, even coating. This method not only provides excellent adhesion and coverage but also minimizes the chances of coating defects, making it a preferred choice for many manufacturers.
Applications of EP Coating in Various Industries
The versatility of EP Coating allows it to be utilized across various sectors, adapting to unique requirements and challenges. Some of the prominent applications include:
- Automotive Industry: EP Coating is extensively used in automotive manufacturing for coating car bodies and parts. The process offers superior corrosion resistance, essential for vehicles exposed to harsh environmental conditions.
- Electronics: In the electronics industry, EP Coating is applied to circuit boards and other components to enhance their insulation properties and protect against moisture and contaminants.
- Industrial Equipment: For machinery and industrial components, EP Coating provides a protective layer that can withstand harsh chemicals and physical wear, increasing longevity and reliability.
- Consumer Goods: Home appliances and various consumer products benefit from EP Coating’s aesthetic appeal and protective qualities, ensuring a longer lifespan and better performance.
Benefits of Using EP Coating
The advantages of EP Coating extend beyond its functional applications. Here are some key benefits:
- Corrosion Resistance: EP Coating provides excellent protection against corrosion, significantly enhancing the lifespan of coated components.
- Uniform Coverage: The application process ensures an even coating across complex geometries, making it ideal for intricate component designs.
- Eco-Friendly Process: Many modern EP Coating formulations utilize water-based paints, which reduces harmful emissions compared to solvent-based systems.
- Enhanced Process Efficiency: The automated nature of EP Coating allows for quicker application and curing times, streamlining production processes and reducing labor costs.
EP Coating Process Explained
Step-by-Step Procedure for EP Coating
The EP Coating process can be broken down into several integral steps, each contributing to the final quality of the coating:
- Surface Preparation: Before coating, substrates must be thoroughly cleaned and prepped to remove any grease, dirt, or oxidation. This may involve rinsing, sandblasting, or chemical treatments.
- Bath Setup: Substrates are submerged in a bath containing an aqueous dispersion of paint and other chemicals. The paint’s composition includes specific resins and pigments tailored to desired properties.
- Electrophoretic Deposition: An electric current is applied, causing charged paint particles to migrate to the substrate’s surface and adhere to it.
- Curing: After deposition, the coated components are cured in an oven to solidify the coating, enhancing its mechanical properties and durability.
- Inspection: Finally, the coated parts undergo rigorous quality control checks to identify any defects or inconsistencies.
Key Materials Used in the EP Coating Process
The success of the EP Coating process is heavily dependent on the materials used. Some critical components include:
- Resins: The type of resin used significantly influences the coating’s final properties, including flexibility and hardness.
- Pigments: These provide the desired color and opacity, but also impact the coating’s durability and stability under UV exposure.
- Solvents: In water-based systems, the amount and type of solvent affect the fluidity and application properties of the paint.
Common Equipment and Tools for EP Coating
The equipment utilized in the EP Coating process includes:
- Electrophoretic Bath: A specialized tank designed to house the coating solution where the electrochemical reaction occurs.
- Power Supply: Provides the electric voltage necessary for the electrophoretic deposition process.
- Ovens: Used for curing the coated components to enhance the coating’s physical properties.
Comparing EP Coating with Other Coating Techniques
EP Coating vs. Powder Coating
While both EP Coating and powder coating serve similar purposes, their processes and results differ significantly:
- Application Method: Powder coating involves electrostatically spraying dry powder onto a surface, while EP Coating uses an aqueous-based medium.
- Curing Process: Powder coatings require a higher curing temperature, while EP Coating generally can cure at lower temperatures.
- Thickness of Coating: EP Coating typically results in a thinner layer compared to powder coating, allowing better fit in assemblies where space is restricted.
Unique Properties of EP Coating Over Traditional Methods
The distinct properties of EP Coating set it apart from traditional methods. Notably, its electrochemical adhesion leads to:
- Superior Coverage: EP Coating can effectively cover recessed areas, ensuring uniformity even on complex shapes.
- Reduced Need for Manual Labor: The automation of the coating process minimizes any variability associated with human application, providing consistent quality.
- Less Waste: Due to its efficient application method, EP Coating generates less overspray and material waste compared to other painting techniques.
Industry Best Practices for Selecting Coating Techniques
Choosing the right coating technique is vital for achieving desired outcomes. Best practices include:
- Understanding the End Use: Consider the environment and application of the coated part to select a method that meets durability and aesthetic requirements.
- Evaluating Cost-Effectiveness: Analyze the overall costs associated with material input, labor, and long-term performance to determine the best value option.
- Testing and Feedback: Pilot testing different methods and gathering feedback can help refine subsequent applications and surface finishes.
Addressing Challenges in EP Coating Implementation
Common Issues Faced During EP Coating
Various challenges may arise during the EP Coating process, including:
- Inconsistent Coating Thickness: Variations in electric current or inadequate preparation can lead to uneven coating.
- Contamination: Particles from the environment can interfere with the deposition process, affecting adhesion and appearance.
- Equipment Failures: Malfunctions in the power supply or curing equipment can disrupt production and cause rework.
Solutions to Enhance Coating Performance
To mitigate common issues in EP Coating, manufacturers can implement the following solutions:
- Regular Maintenance: Consistent check-ups and servicing of equipment can prevent breakdowns and maintain production flow.
- Strict Quality Control: Implementing rigorous inspection and testing processes can help identify issues early and improve overall quality.
- Training and Skill Development: Upskilling staff can enhance their understanding of the coating processes and ensure proper techniques are used.
Case Studies: Successful EP Coating Implementations
Numerous companies have successfully integrated EP Coating into their manufacturing processes, resulting in heightened performance and customer satisfaction. For example:
In the automotive sector, a leading car manufacturer adopted EP Coating to enhance the durability and aesthetics of their vehicle bodies. The result was not only improved corrosion resistance but also a reduction in warranty claims related to paint defects, leading to significant cost savings and improved customer trust.
Another case study involves an electronics manufacturer that implemented EP Coating for circuit boards, significantly enhancing the protection against moisture intrusion, thereby increasing the reliability of their products in high-humidity environments.
The Future of EP Coating Technology
Emerging Trends in EP Coating Applications
As technology continues to advance, several emerging trends are shaping the future of EP Coating:
- Smart Materials: The integration of smart materials in coatings can allow for self-healing properties and adaptive performance based on environmental conditions.
- Nanotechnology: The use of nanomaterials in coatings can enhance properties like UV resistance, scratch hardness, and antimicrobial performance.
- Modular Coating Systems: Systems that allow for easy interchange of coating types can provide manufacturers with heightened flexibility in production.
Innovations in EP Coating Materials and Processes
Research and development are paving the way for innovative materials and methods that improve efficiency and performance in EP Coating:
- Environmentally Friendly Formulations: Continued efforts to formulate eco-friendly coatings, such as those utilizing bio-based polymers, are expected to grow.
- Process Automation: Advancements in automated coating systems are enhancing efficiency, reducing lead times, and improving coating consistency.
- Real-Time Monitoring: New technologies allowing for real-time monitoring of coating thickness and quality during production are being developed, ensuring optimal outcomes.
Environmental Considerations in EP Coating
As industries focus on sustainability, the EP Coating process is adapting to meet environmental considerations:
- Water-Based Coatings: Transitioning to water-based systems reduces the emission of volatile organic compounds (VOCs) into the atmosphere.
- Recycling and Waste Reduction: Implementing strategies for recycling excess material and reducing waste is becoming increasingly important in the coating process.
- Energy Efficiency: Innovations aimed at reducing energy consumption during production and curing processes are being prioritized by manufacturers.