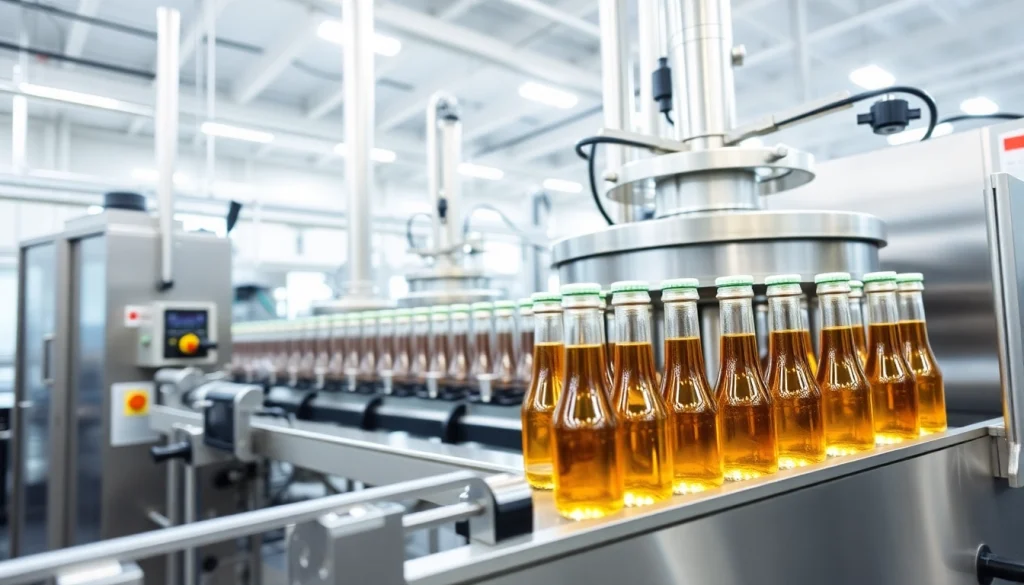
Understanding Filling Machines
What is a Filling Machine?
A filling machine is a device designed to accurately fill containers with liquids, powders, granules, or other substances. Filling machines are vital in industries such as food and beverage, cosmetics, pharmaceuticals, and more, ensuring that products are dispensed efficiently and in precise amounts. These machines significantly improve production speed and consistency, reducing the likelihood of human error in the packaging process. They can vary widely in complexity, from simple, manual systems to high-tech automated solutions.
Types of Filling Machines Available
Filling machines can be categorized based on their operational mechanisms, types of containers they serve, and the products they dispense. Here are the primary types:
- Gravity Fillers: Suitable for thin, free-flowing liquids, gravity fillers dispense products through gravity. These machines are simple and cost-effective but may not be suitable for all products.
- Piston Fillers: Utilizing a piston mechanism, these machines are ideal for thicker liquids and pastes. They provide high accuracy and are commonly used in the food, cosmetic, and pharmaceutical industries.
- Vacuum Fillers: Perfect for filling bottles and jars with products like liquids or creams. Vacuum fillers create a vacuum that draws the product into the container, ensuring accurate and spill-proof filling.
- Pump Fillers: These devices use a pump to transfer liquids and are versatile for various viscosities. They are typically automated, offering high-speed filling options.
- Time Gravity Fillers: These machines utilize a timed mechanism to dispense a specific volume of liquid. They are suitable for various liquid products and are known for their speed and efficiency.
Key Components of a Filling Machine
Understanding the fundamental components of a filling machine is essential for selecting the right equipment for your needs. Key components include:
- Filling Nozzles: These are crucial for controlling the flow of the product into the container. They can be designed for different flow rates and product types.
- Control System: An electronic or mechanical control system regulates the filling process, ensuring consistency and accuracy in each fill.
- Conveyor System: This system moves containers into position for filling and can significantly speed up the operation.
- Product Reservoir: The storage area where the product is held before being dispensed. This can vary in size based on production needs.
- Frame and Chassis: The structural component that houses all parts, ensuring stability and durability.
Choosing the Right Filling Machine Supplier
Evaluating Supplier Credentials
When selecting a filling machine supplier, verifying their credentials is critical. This involves checking their industry experience, reputation, and the quality of their products. Look for suppliers with certifications that demonstrate compliance with industry standards, such as ISO certifications, which verify the company adheres to specific quality management principles.
Importance of Customer Support
Exceptional customer support is vital when choosing a filling machine supplier. After-sales support can significantly impact machine performance and longevity. Ensure that the supplier offers comprehensive warranty options, maintenance services, and quick response times to issues that may arise. Testimonials from past clients can provide valuable insights into what to expect from their customer service. A reliable supplier should also provide training on how to operate and maintain the machine effectively.
Assessing Machine Customization Options
Not all filling machines will suit every application. Therefore, consider suppliers that offer customization options tailored to your specific operational needs. The ability to modify the machine for different container sizes, product viscosities, and throughput rates can lead to increased efficiency and a better return on investment. Discuss your unique requirements with potential suppliers to ensure they can meet your specific application needs.
Industry Applications of Filling Machines
Beverage Bottling
Filling machines are extensively used in the beverage industry for bottling various drinks, from water to carbonated soft drinks. Reliable precision is crucial to avoid overfilling or underfilling, which can lead to product waste and dissatisfaction among consumers. Manufacturers are increasingly investing in automated filling systems that offer rapid production rates and consistent quality control
Cosmetics and Personal Care
Filling machines in the cosmetics industry are designed to fill containers with products such as creams, lotions, and serums. These machines can be adapted to handle various viscosities and are often equipped with nozzles that minimize product waste and ensure cleanliness during the dispensing process. The aesthetic appeal of the packaging is also significant, so some filling machines incorporate advanced features to maintain the integrity of the product during filling.
Pharmaceutical Packaging
In the pharmaceutical industry, filling machines play a critical role in ensuring that medications are dispensed accurately and safely. Compliance with stringent safety regulations is paramount, and suppliers must ensure their machines adhere to industry standards like Good Manufacturing Practices (GMP). The machines often feature advanced technology such as automated cleaning systems and precise dosing capabilities to maintain the quality and safety of pharmaceutical products.
Best Practices for Maintaining Filling Machines
Regular Maintenance Checks
Routine maintenance checks are essential for keeping filling machines in optimal condition. Regular inspections can identify potential issues before they escalate, allowing for timely repairs and reducing downtime. Operators should establish a maintenance schedule based on the machine’s usage and manufacturer’s recommendations, ensuring routine tasks such as lubrication, alignment checks, and component replacements are performed consistently.
Cleaning Protocols
A clean filling machine ensures the safety and quality of the products being dispensed. Establishing thorough cleaning protocols will not only protect the equipment but also comply with health and safety regulations. Different products will have varying cleaning requirements; thus, operators should follow specific guidelines for cleaning solutions suitable for the substances they handle. Implementing automated cleaning systems can further enhance hygiene while reducing labor costs.
Replacement of Key Parts
Over time, certain components of filling machines will wear down and require replacement. Regularly inspecting parts such as nozzles, pumps, and seals can preemptively address any issues that may arise due to wear and tear. Stocking essential spare parts can maintain efficiency, enabling quick replacements and minimizing downtime during production halts.
Future Trends in Filling Machine Technology
Automation and Smart Technologies
As industries develop, automation continues to play an increasingly significant role in filling machine technology. Smart filling machines equipped with sensors and IoT capabilities can monitor their performance in real-time. This technology allows for data collection, predictive maintenance, and operational efficiencies that were previously unattainable. Businesses can optimize their production lines based on data-driven insights, leading to improved output and lower energy costs.
Sustainability in Packaging
With the growing global emphasis on sustainability, filling machine suppliers are adopting eco-friendly practices. Companies are designing machines that minimize waste and support recyclable packaging materials. Additionally, advancements in technology facilitate the use of biodegradable, reusable, or refillable containers, aligning with consumer demand for environmentally responsible products.
Advancements in Efficiency and Accuracy
The future of filling machines promises enhanced efficiency and accuracy through constant innovation. Emerging technologies, such as artificial intelligence and machine learning, will allow machines to learn from their surroundings and improve their performance over time. Predictive algorithms can optimize filling processes by adjusting settings based on real-time conditions, leading to extremely precise fills and reduced errors.