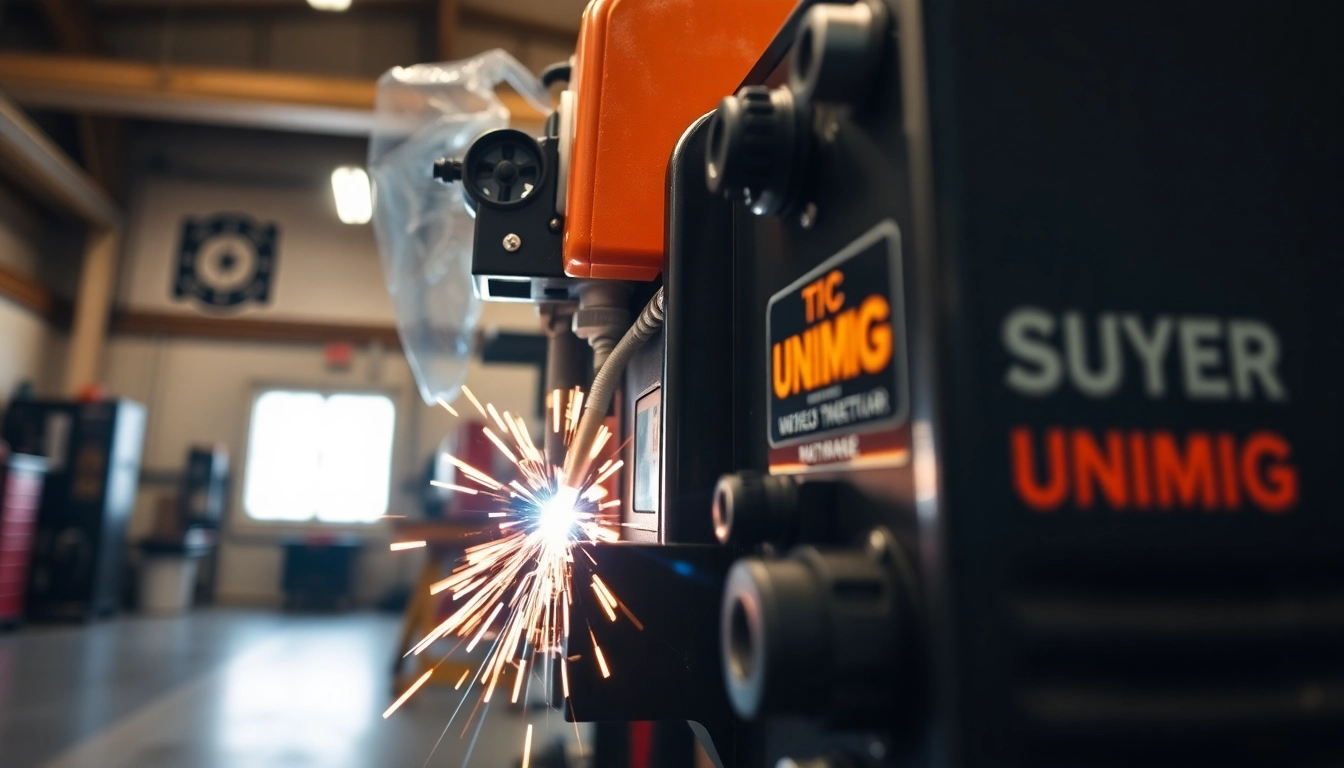
Understanding the Unimig TIG Welder
The world of welding has transformed significantly over the years, with various techniques and equipment catering to both amateur and professional welders alike. Among these advancements, the unimig tig welder stands out as a popular choice for those looking to achieve precision and quality in their welding projects. This article delves into the intricacies of Unimig TIG welders, enhancing your understanding of their functionality, benefits, and key considerations for selection.
What is TIG Welding?
TIG (Tungsten Inert Gas) welding, also known as Gas Tungsten Arc Welding (GTAW), is a versatile welding process that employs a non-consumable tungsten electrode to produce the weld. The process relies on a shielding gas (commonly argon) to protect the weld area from atmospheric contamination, ensuring a clean and strong weld joint.
TIG welding is distinguished by its ability to weld a variety of metals, including stainless steel, aluminum, and copper alloys, making it a vital technique in industries such as automotive, aerospace, and fabrication. The method allows for greater precision, control, and a neat finish, appealing to professionals and hobbyists alike.
Key Features of Unimig TIG Welders
Unimig TIG welders are known for their innovative features, which enhance usability, versatility, and effectiveness. Here are some of the standout features:
- AC/DC Capability: Many models, such as the Unimig Razor series, offer AC/DC functionality, enabling welding on both aluminum (AC) and steel (DC).
- High-Frequency Start: This feature eliminates the need to touch the tungsten electrode against the workpiece, minimizing contamination and prolonging electrode life.
- Pulse Welding: Adjustable pulse settings allow for better control over heat input and can be particularly useful for thin materials.
- Advanced Controls: Digital displays and user-friendly interfaces simplify adjustments for voltage and current, ensuring more precise welding conditions.
Benefits of Using Unimig TIG Welders
The advantages of using Unimig TIG welders extend far beyond their advanced features. Here are some key benefits:
- Precision and Control: The ability to fine-tune the welding arc results in stronger weld joints and cleaner finishes.
- Versatility: Unimig TIG welders can handle various materials, making them suitable for a wide array of applications, from art sculptures to mechanical components.
- Low Heat Input: TIG welding generally produces less distortion in the base metal, preserving the integrity of thin sections.
- Minimal Fumes and Pollution: The use of inert gas means fewer fumes are produced, promoting a healthier working environment.
Choosing the Right Unimig TIG Welder for Your Needs
Selecting the appropriate Unimig TIG welder involves understanding various models and their intended uses. This section will explore different models, provide a comparative analysis of the Viper and Razor series, and highlight critical factors to consider before making a purchase.
Different Models of Unimig TIG Welders
Unimig offers several models that cater to different skill levels and project requirements. Here are some of the notable models:
- Unimig Viper 180 AC/DC: Ideal for hobbyists and light fabrication tasks, this welder provides excellent performance for both DC and AC welding, making it versatile for various materials.
- Unimig Razor 200 AC/DC: A professional-grade machine designed for more demanding applications, offering advanced features such as pulse functions and extensive output control.
- Viper Multi 195 MAX: This model caters to users requiring TIG, MIG, and stick welding capabilities in one device, providing an excellent all-rounder for diverse projects.
Comparative Analysis: Viper vs. Razor Series
When considering Unimig TIG welders, the choice between the Viper and Razor series is significant. Each series has its strengths, appealing to different user needs:
Viper Series:
The Viper series is geared toward entry-level to intermediate users, featuring user-friendly setups with comprehensive guides. The machines often emphasize ease of use and portability, making them suitable for personal and light industrial applications.
Razor Series:
In contrast, the Razor series targets professional welders, offering advanced features, including programmable settings and extensive control for demanding tasks. These welders cater to industries requiring high durability and performance standards, such as automotive manufacturing and heavy equipment maintenance.
Factors to Consider When Buying a TIG Welder
Before purchasing a Unimig TIG welder, consider the following factors:
- Welding Application: Determine the materials and thicknesses you will be welding. Some models are better suited for specific applications.
- Power Requirements: Ensure the welder matches your power supply capabilities—varying models may require single or three-phase power.
- Budget: Establish a budget that not only includes the welder but also the necessary accessories and consumables.
- Portability: If you’ll be moving the welder between job sites or projects, consider the weight and ease of transport.
Essential Accessories for Unimig TIG Welding
To maximize the efficiency and quality of your welding, acquiring essential accessories is crucial. The right tools can enhance your welding experience significantly.
Must-Have Tools for Beginners
For those just starting in TIG welding with a Unimig welder, certain tools are indispensable:
- Tungsten Electrodes: Choose the right tungsten type based on the materials you’ll be welding—thoriated for steel and pure or zirconiated for aluminum.
- Welding Helmet: Invest in a quality welding helmet that offers proper UV protection and a good view of the workpiece.
- Welding Gloves: Heat-resistant gloves will protect your hands from extreme temperatures and spatter.
- Gas Lens: A gas lens can improve gas flow, providing better shielding and reducing contamination.
Safety Equipment and Best Practices
Safety should be a top priority when welding. Here are essential safety equipment and best practices:
- Personal Protective Equipment (PPE): Always wear appropriate PPE, including gloves, helmets, and protective clothing tailored for welding.
- Ventilation: Ensure your workspace is well-ventilated to dissipate fumes and gases produced during welding.
- Fire Safety: Keep a fire extinguisher nearby and maintain a clear work area free from flammable materials.
Welding Consumables for Optimal Performance
Using high-quality consumables is essential for yielding optimal results. This includes:
- Filler Rods: Choose filler materials that match or complement the base metals for a coherent weld.
- Shielding Gas: Select the appropriate shielding gas blend based on the welding application (for instance, argon is ideal for aluminum).
Practical Techniques for Effective TIG Welding
Mastering practical welding techniques can significantly improve the quality of your welds with a Unimig TIG welder. This section covers setup, techniques, and troubleshooting tips.
Setting Up Your Unimig TIG Welder
A proper setup is crucial for successful TIG welding. Follow these steps:
- Assemble Your Equipment: Connect the gas and ensure the regulator is functioning properly.
- Select the Proper Tungsten Size: Use the correct diameter of tungsten electrode according to your welding material.
- Adjust Welding Parameters: Set the voltage, current, and pulse settings according to the material thickness and type.
Common Welding Techniques and Applications
To ensure effective welds, familiarize yourself with common techniques:
- Weaving Technique: Useful for wide welds, combining a straight and side-to-side motion.
- Stringer Bead Technique: Ideal for thin materials, maintaining a straight line for heat concentration.
- Banking Technique: A more advanced technique where the welder banks on either side to increase coverage.
Applications of TIG welding include:
- Aerospace component fabrication
- Automotive repairs and modifications
- Pipework and pressure vessels
Troubleshooting Common Issues
Even experienced welders can encounter issues. Here are some common problems and solutions:
- Weld Contamination: Ensure the work area is clean and free of oil and dirt.
- Inconsistent Arc: Check gas flow, electrode condition, and ensure proper settings are used.
- Poor Penetration: Increase travel speed or adjust the current settings to better suit the material thickness.
Final Thoughts and Resources
Welding with a Unimig TIG welder can significantly enhance your metalworking projects, allowing for greater precision and efficiency. By understanding the features, models, and best practices, you will be well on your way to mastering TIG welding.
Further Learning and Training Resources
Continuing education is vital for any welder. Look for resources such as:
- Online TIG welding courses
- Welding workshops or community colleges
- Instructional videos on platforms like YouTube
Community and Online Support for TIG Welders
Joining a community of welders can provide support, tips, and a platform for knowledge exchange. Consider:
- Online welding forums and social media groups
- Local welding clubs or workshops
- Consulting with experienced welders in your network
Why Unimig Stands Out in the Welding Industry
Unimig has established itself as a leading brand in the welding market due to its commitment to quality and innovation. Their TIG welders incorporate the latest technology and are designed with user needs in mind, ensuring that both beginners and professionals have access to reliable and effective equipment.