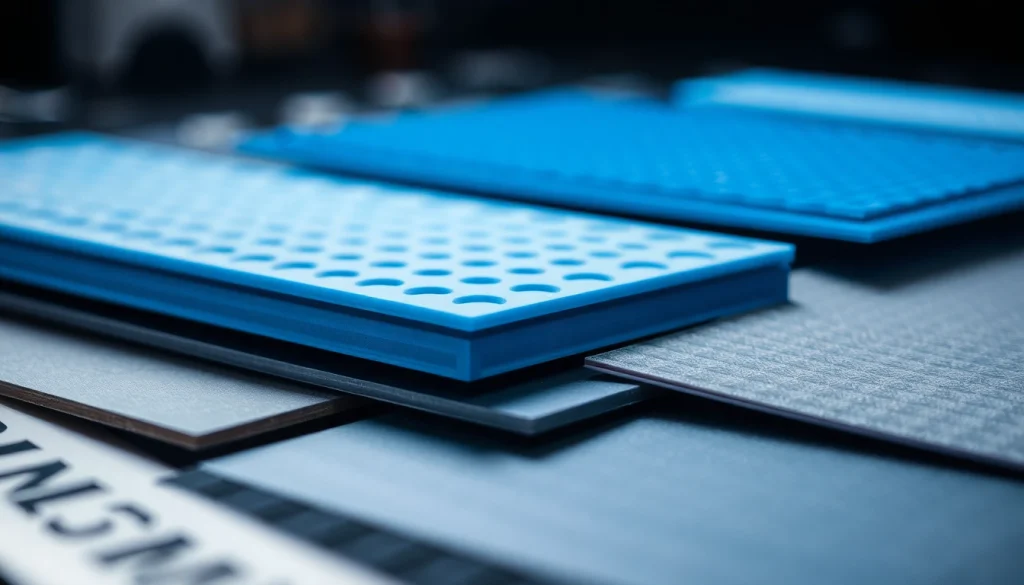
Understanding Thermal Management Materials
In the fast-paced world of electronics, maintaining optimal temperatures is paramount for performance and longevity. This is where thermal management materials step in. These materials play a critical role in heat dissipation, ensuring electronic components operate efficiently without overheating. In this article, we will explore the various aspects of thermal management materials, their importance, applications, and advancements that are shaping the future of electronics.
What Are Thermal Management Materials?
Thermal management materials encompass a variety of substances designed to transfer, dissipate, or contain heat. As electronics become smaller and more powerful, managing heat effectively becomes increasingly complex. These materials can range from thermal interface materials (TIM) to advanced films and composites, each tailored to specific applications and heat management challenges.
Importance of Thermal Management in Electronics
The significance of thermal management in electronics cannot be overstated. Excess heat can lead to a myriad of problems, including reduced performance, shorter lifespan of components, and potential failure of electronic devices. Proper thermal management ensures:
- Improved reliability and lifespan of components.
- Enhanced performance, allowing devices to operate at full capacity.
- Prevention of thermal runaway, an essential safety concern in modern electronics.
With the rise of compact and power-hungry devices, efficient thermal solutions are more critical than ever.
Types of Thermal Management Materials
Thermal management materials can be broadly categorized into several types, each serving unique functions:
- Thermal Interface Materials (TIM): These materials fill the microscopic gaps between heat-generating components and heat sinks. Common examples include thermal pastes, pads, and gels, which improve thermal contact and conductivity.
- Phase Change Materials (PCMs): PCMs absorb and release heat as they change states from solid to liquid and vice versa, making them ideal for temperature regulation in varying conditions.
- Gap Fillers: These materials, often in the form of soft pads or gels, are used in applications where there are uneven surfaces, ensuring uniform heat transfer.
- Heat Spreaders: Made of high thermal conductivity materials, such as copper or aluminum, heat spreaders distribute heat from hot spots across a larger area, preventing localized overheating.
- Thermal Adhesives: These double-function materials bond components while simultaneously conducting heat away from them, providing structural support in addition to thermal management.
Key Applications of Thermal Management Materials
Applications in Consumer Electronics
Consumer electronics such as smartphones, laptops, and gaming consoles demand robust thermal management solutions. As devices become thinner and packed with high-performance components, managing heat efficiently is crucial. For example, modern gaming consoles use advanced thermal interface materials to maintain optimal temperatures during intense gaming sessions, preventing throttling and ensuring a smooth user experience.
Industrial and Automotive Uses
The industrial sector heavily relies on thermal management to ensure the functionality and reliability of equipment. Heavy machinery exposed to extreme conditions often employs thermal materials to protect vulnerable components. In the automotive industry, electric vehicles (EVs) utilize thermal management materials for battery cooling to enhance performance and safety, ensuring that battery health is maintained even under demanding conditions.
Specialized Applications in Aerospace and Defense
Aerospace and defense industries present unique thermal challenges due to extreme environmental conditions. Thermal materials are crucial in spacecraft, where they help manage heat during re-entry or when exposed to the vacuum of space. Additionally, military equipment uses specialized thermal management solutions to maintain operational readiness in diverse climates.
Choosing the Right Thermal Management Material
Factors to Consider When Selecting Materials
When selecting thermal management materials, several factors must be considered to ensure optimal performance:
- Thermal Conductivity: High thermal conductivity ensures better heat transfer, essential for efficient thermal management.
- Thickness and Compliance: Suitable thickness allows for effective heat transfer while maintaining compliance with component surfaces for optimal contact.
- Environmental Resistance: Materials must withstand environmental conditions such as humidity, temperature fluctuations, and mechanical stress.
- Adhesion Properties: In applications requiring bonding, the adhesive characteristics of the material can significantly impact performance.
Common Misconceptions About Thermal Materials
Despite their importance, several misconceptions surround thermal management materials:
- “Higher thermal conductivity is always better.” Not all applications require the same level of conductivity. The choice should align with specific thermal management needs.
- “All TIMs are the same.” Different types of TIMs serve distinct purposes; understanding the application requirements is crucial for optimal selection.
- “Thermal management materials are only used in high-performance applications.” Even everyday consumer electronics benefit from appropriate thermal solutions to enhance performance and lifespan.
Performance Metrics for Evaluation
Evaluating the performance of thermal management materials requires specific metrics:
- Thermal Resistance: Lower thermal resistance indicates better performance in transferring heat.
- Compressive Strength: This measures how well the material can maintain performance under mechanical compression, ensuring consistent contact with heat-generating components.
- Operating Temperature Range: Materials must perform effectively within the given operational temperature limits of the application.
Best Practices for Implementing Thermal Management Solutions
Installation Techniques for Effective Performance
Proper installation of thermal management materials is crucial for their effectiveness. Best practices include:
- Surface Preparation: Clean and prepare surfaces to remove contaminants and achieve optimal adhesion.
- Even Application: Apply thermal interface materials evenly to prevent air gaps that can hinder performance.
- Follow Manufacturer Guidelines: Adhere to specifications regarding thickness and application methods to ensure optimal results.
Maintenance and Testing of Thermal Materials
Regular maintenance and testing of thermal management solutions can significantly affect their longevity and performance. Implementing a routine check-up for potential degradation can prevent catastrophic failures. Techniques for maintenance include:
- Visual Inspections: Look for signs of wear, cracking, or deterioration in thermal interface materials.
- Thermal Imaging: Use thermal cameras to visualize heat distribution and locate hotspots that may indicate thermal management issues.
Case Studies: Successful Implementations
Several successful implementations of thermal management materials highlight their importance:
- Product X: Faced overheating issues, leading to device failures. By integrating a new thermal interface material, the product improved heat dissipation efficiency by 30%, resulting in enhanced performance and customer satisfaction.
- Electric Vehicle Y: Required reliable thermal management for its battery system. After employing phase change materials, battery life increased by 15%, showcasing the critical role of thermal materials in EV design.
Future Trends in Thermal Management Materials
Innovations in Material Science
The field of thermal management materials is evolving rapidly due to advancements in material science. Innovations include the development of:
- Nanomaterials: Utilizing nanoparticles to improve thermal conductivity and provide lightweight solutions.
- Smart Materials: These materials respond to temperature changes, optimizing thermal management dynamically.
- Graphene: With its excellent thermal properties, graphene is being explored for next-generation heat management solutions in high-performance electronics.
Sustainability in Thermal Management
As the demand for eco-friendly solutions grows, the thermal materials industry is making strides toward sustainability. Green materials, including biodegradable and recyclable options, are being developed to minimize environmental impact. These initiatives help address the industry’s carbon footprint while still meeting performance specifications.
Emerging Technologies and Their Impact
Emerging technologies, such as 5G and Internet of Things (IoT) devices, are driving demands for innovative thermal management solutions. These devices often require materials that are not only efficient but also lightweight and compact. Additionally, as the trend toward miniaturization continues, advanced solutions that integrate thermal management into chip designs are being explored.