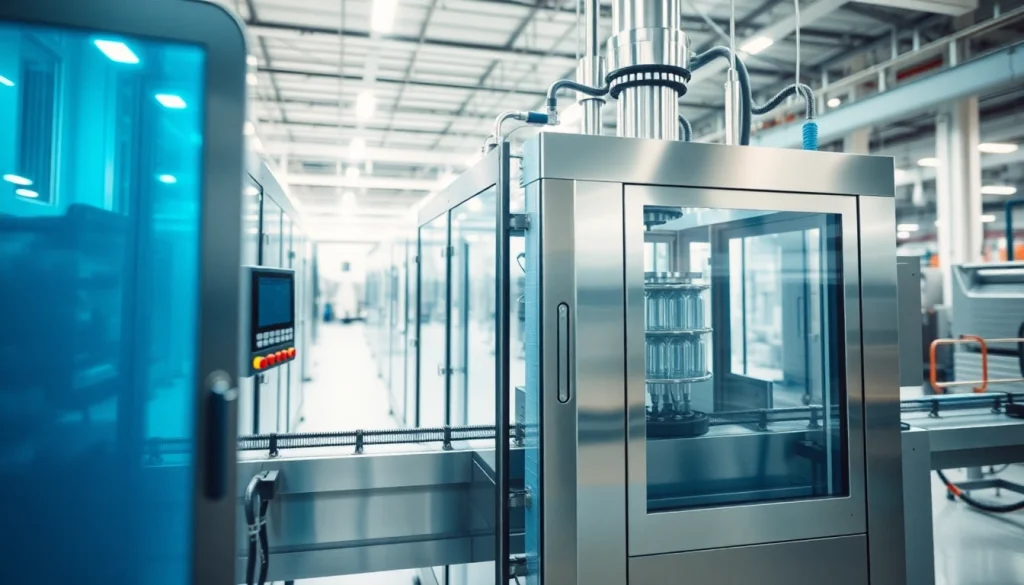
Understanding Your Filling Machine Needs
In the competitive landscape of manufacturing, selecting the right equipment is crucial for optimizing production efficiency and meeting demand. A key component of beverage, pharmaceutical, and various industrial processes is the filling machine. Understanding your filling machine needs is the first step in making an informed purchasing decision. It is imperative to assess factors such as production volume, types of filling machines available, and industry-specific applications before proceeding. For businesses seeking expertise, working with a reputable Filling Machine Supplier can streamline this process.
Assessing Production Volume Requirements
Your production volume requirements will greatly influence your choice of filling machine. Different machines cater to varied production scales, ranging from small batch operations to large-scale industrial applications. To determine your needs effectively, consider the following:
- Daily Production Output: Calculate how many units you need to produce each day. This metric will help identify whether you need a semi-automatic filling machine capable of handling smaller volumes or a fully automated system designed for high throughputs.
- Product Transformation: Evaluate how often you need to change over products. High product variety can necessitate versatile filling machines that can be adjusted quickly, while consistent production can allow for specialized systems.
- Future Scalability: Take into account future production goals. If you anticipate growth or increased demand, investing in a machine that can scale with your operations is wise.
Types of Filling Machines Available
Understanding the available types of filling machines is essential for aligning your production needs with the right technology. Different technologies suit various products and applications. Below are the primary types:
- Piston Filling Machines: These machines utilize a piston mechanism to dispense precise volumes of liquids. They are excellent for thick, viscous products, including sauces and creams.
- Vacuum Filling Machines: Ideal for thin liquids, these machines use vacuum pressure to control the filling process, ensuring minimal spillage and an accurate fill.
- Gravity Filling Machines: This type relies on gravity to fill containers, perfect for free-flowing liquids. It is often used in the beverage industry.
- Pump Filling Machines: Versatile in nature, they can handle a range of product viscosities and are used for liquids that require specific handling.
- Auger Filling Machines: Typically used for powders and granulated materials, auger fillers can efficiently deliver specific quantities.
Industry-Specific Applications
The applications of filling machines can vary significantly across industries. Below are examples highlighting how different sectors utilize filling technology:
- Food and Beverage Industry: Specific filling machines cater to applications such as bottling liquids (water, juice, alcoholic beverages) and packaging solids (sugar, flour).
- Pharmaceutical Industry: Precision and compliance are paramount; filling machines must adhere to stringent regulations while ensuring cleanliness and accuracy.
- Cosmetics and Personal Care: Filling machines in this sector often need to accommodate varying viscosities and container types, ranging from lotions to perfumes.
- Chemical Industry: Here, machines must withstand corrosive substances and have strong durability, often requiring specialized materials.
Choosing the Right Filling Machine Supplier
Once you’ve established your filling needs, the next step is selecting a filling machine supplier that aligns with your business objectives. The right supplier will not only offer quality equipment but also provide support throughout the buying process and beyond.
Key Factors to Consider
When evaluating potential suppliers, consider several critical factors:
- Product Range: A supplier offering a comprehensive range of machines will be better equipped to meet your specific needs, whether you require a specialized solution or standard equipment.
- Innovation and Technology: Consider suppliers that invest in advanced technology to improve equipment efficiency, automation, and user interface.
- Manufacturing Standards: Ensure the supplier adheres to industry standards such as ISO certifications, reflecting their commitment to quality.
- Customer Reviews and Case Studies: Research past client experiences to gauge supplier reliability and service standards.
Evaluating Supplier Reputation and Experience
A supplier’s reputation can significantly affect your operations. Look for:
- Years of Experience: Established suppliers tend to have more refined processes and insights into market needs.
- Industry Recognition: Awards or acknowledgments can indicate credibility and quality.
- Customer Retention Rates: High retention often reflects satisfaction and trust in the supplier’s offerings.
Understanding Service and Warranty Options
Finally, it’s essential to understand the warranty and support options provided by your supplier:
- Warranty Period: A longer warranty period often indicates higher product quality and reliability.
- After-Sale Support: Evaluate the availability of technical support, training, and maintenance services.
- Availability of Spare Parts: Ensure the supplier offers timely access to spare parts to avoid downtime during unexpected maintenance issues.
Top Features of Modern Filling Machines
Modern filling machines come equipped with advanced features designed to improve functionality, efficiency, and ease of use. Understanding these features can help you make an informed purchase.
Automation and Control Systems
One of the standout features of contemporary filling machines is the incorporation of automation and sophisticated control systems. These features include:
- Touchscreen Interfaces: User-friendly controls enhance operator efficiency and training time.
- Programmable Logic Controllers (PLCs): These devices manage machine operations, allowing customizable settings for various products and speeds.
- Real-Time Monitoring: Operators can receive immediate feedback on the filling process, ensuring issues are addressed proactively.
Integration with Existing Production Lines
Compatibility with existing production lines is crucial for smooth operations. Modern filling machines are designed to work seamlessly with:
- Capping and Labeling Machines: Integrated systems streamline packaging processes, reducing manual handling and potential errors.
- Conveyor Systems: Efficient transport of filled containers into secondary processes.
- Quality Control Stations: To immediately check fill accuracy and product integrity before distribution.
Maintenance and Support Considerations
Maintenance is a vital aspect of equipment longevity. When selecting a filling machine, ensure it is:
- Low Maintenance: Machines designed for easy access to components can significantly reduce downtime during servicing.
- Accompanied by Documentation: Comprehensive operator manuals and guides facilitate easier troubleshooting and parts replacement.
- Supported by Supplier Services: Partnerships with suppliers for regular maintenance checks can extend equipment life and performance.
Cost Considerations for Filling Machines
Cost is a critical factor in any purchasing decision. Understanding the financial implications of filling machine investments can help you mitigate risks and maximize returns.
Initial Investment vs. Long-Term Savings
While the initial cost of a filling machine can be significant, consider the long-term savings associated with:
- Higher Efficiency: Automated systems reduce the need for manual labor and have faster filling speeds, leading to increased productivity.
- Lower Error Rates: Machines equipped with precise filling technology minimize waste, which can save on raw materials over time.
- Energy Efficiency: Newer models are often designed to consume less power, contributing to reduced operational costs.
Financing Options for Businesses
Many suppliers offer financing solutions that can ease the burden of initial investments. Consider these options:
- Leasing vs. Purchasing: Leasing may provide access to advanced technology with lower upfront costs, while purchasing may offer long-term savings.
- Manufacturer Financing Programs: Some suppliers provide tailored financing solutions based on your company’s cash flow considerations.
Cost of Maintenance and Spare Parts
When budgeting for your filling machine, don’t overlook ongoing maintenance costs. These include:
- Regular Maintenance Checks: Scheduled service intervals to keep equipment running smoothly.
- Spare Parts Replacement: Costs associated with replacing worn-out components can add up; ensure parts are readily available from your supplier.
- Unexpected Repairs: Allocating a budget for emergency repairs can prevent production stoppages due to equipment failure.
Future Trends in Filling Technology
The landscape of filling technology is continuously evolving, bringing innovative solutions that enhance efficiency, accuracy, and sustainability. Staying abreast of these trends can inform your purchasing decisions.
Advancements in Filling Accuracy
Current innovations focus on enhancing the precision of filling processes. Machine learning algorithms can analyze data patterns to improve:
- Fill Levels: Ensuring products are filled to exact specifications reduces waste and enhances consumer satisfaction.
- Quality Control Measures: Real-time monitoring systems promote immediate corrections in the filling process, thus maintaining quality standards.
Sustainability Practices in Machine Manufacturing
As industries lean towards sustainability, modern filling machines are being designed with eco-friendly manufacturing practices. This involves:
- Energy-Efficient Systems: Incorporating energy-saving technologies reduces carbon footprints.
- Recyclable Materials: Using sustainable materials in production contributes to environmental responsibility.
- Waste Management Solutions: Machines designed to minimize waste during production processes not only save costs but also benefit the planet.
The Role of IoT in Filling Operations
Internet of Things (IoT) technology is increasingly integrated into filling machines, leading to transformative benefits such as:
- Remote Monitoring: Access equipment performance data from anywhere, enabling quick responses to production issues.
- Data Analytics: Utilize data gathered from machines to optimize operations and predict maintenance needs.
- Enhanced Security: IoT can bolster system security, protecting sensitive production data.